S2K Commerce - Products Dropdown

- ${title}
S2K Commerce - Shopping Cart

- ${title}
S2K Commerce - Order Entry

- ${title}
Please note, from February 27th to March 7th, credit card processing for online orders will be done manually as we transition to new company wide software. If your company has established open terms with EMI, you may supply a purchase order number in the online order form in lieu of a credit card number. You can also convert the items in your cart into a Quote and contact us to complete the order. We will be launching a new website the week of March 10th.
End of Arm Tooling (EOAT) Experts
Whether you need only 2 vacuum cups or over 100 custom EOATs engineered and built, EMI has the experience that thousands of customers have come to rely on for their successful End of Arm Tooling needs. We’ve got an enormous stock and broad range of EOAT components, knowledgeable engineering support, talented assembly technicians, and in-house manufacturing. EMI does EOAT in a big way! EMI’s in-house End of Arm Tooling engineering department of 20 EOAT engineers is dedicated to supporting all your needs for End of Arm Tooling products. No question is too small and no project has been too large. Since 2001 we’ve been helping users select everything from the right vacuum cups to engineering complete project sets. We’re easily accessible, friendly, and helpful. Give us a call and let us help you.
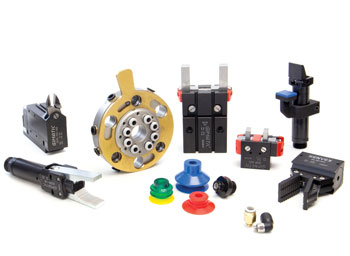
End of Arm Tooling Components
In-stock inventory in Ohio ready to ship the same day. Easy online ordering including Related Items and Replacement Parts.
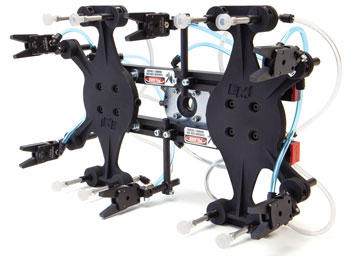
Engineering and Build Service
Get expert assembly and save time! You can choose to build the EOAT yourself, or you can take advantage of EMI’s EOAT Build Service.

3D Printing for EOAT
Custom 3D printed gripper fingers from EMI are ideal for use on EOAT in plastics as well as on collaborative robot grippers. We think you’ll find EMI’s 3D printing is affordable and fast.
EOAT and Conveyor Automation Systems for Cobots
EMI’s years of experience in automation applications prove that we can provide the perfect solution for a wide variety of industrial End of Arm Tooling (EOAT) and custom cobot gripper kit needs.
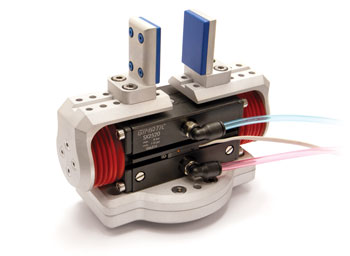
EOAT for Cobots
Our engineers have outfitted many of our industry-proven pneumatic and electric grippers to easily adapt to, and maximize the high repeatability of Cobots.
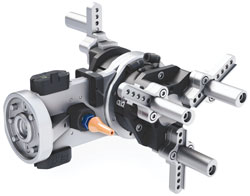
Machine Tending from EMI
Whether you're new to automation or redeploying and existing robot/collaborative robot, our machine tending kits are ideal for tending CNC mills and lathes.
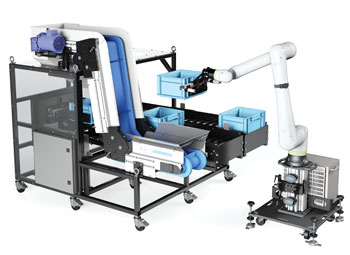
Cobot Ready Conveyors
EMI’s Cobot Ready Conveyors are designed to be integrated with your Universal Robot and allows for easy programming. Using a Doosan, Kuka, Fanuc, or other Collaborative Robot? Contact us to discuss!
Conveyors and Automation Systems
EMI manufactures custom heavy-duty industrial conveyor systems.

Conveyor Automation Systems
EMI will design and build an automation system that meets your requirements and exceeds your expectations. Contact us today to get your free quote.
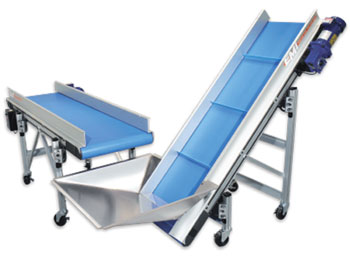
Belt Conveyors
EMI can deliver a sturdy, lightweight conveyor system that can be customized to suit your exact automation needs. Three styles of power transmission - Belt drive is standard. Direct drive and chain drive are also available.
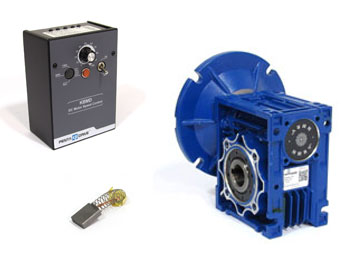
Spare Parts and Maintenance
Our most common conveyor replacement parts are online. Our sales and service department can help you find replacement parts for all EMI conveyor makes and models. Maintenance videos now on YouTube!
Injection Molding Supplies
We offer the best Injection Molding Components available. As one of the world’s largest manufacturers of end-of-barrel components and accessories, we have compiled a long list of problem-solving products.
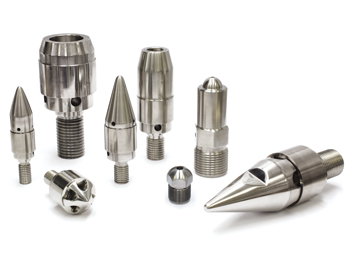
Non-Return Valves and Nozzles
Hundreds of End of Barrel components for popular sizes and machine makes are in stock and ready for immediate shipment. EMI will also custom manufacture ring valves, ball checks and nozzles.
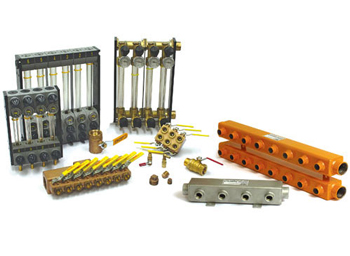
Water Flow Management
Water manifolds are available in heavy-duty powder-coated steel, stainless steel, aluminum, and bronze. We also supply water flow regulators, brass ball valves, nipples, and quick couplings to complete your installation.
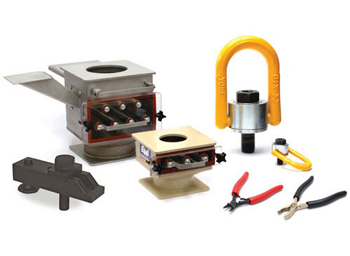
Injection Molding Supplies
We know how important up-time is to your productivity, so we stock the most popular sizes and models of Injection Molding Supplies to give you service when you need it the most.
EMI Literature and CAD Files
We make it easy; Online Catalogs with pricing, Interactive Forms, CAD File Downloads, & more available without needing a login!
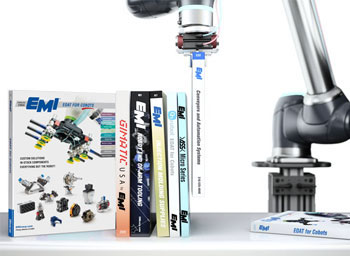
All EMI Catalogs in one place!
Our Interactive catalogs in English and Spanish have pricing, easy internal navigation, and links to e-commerce.
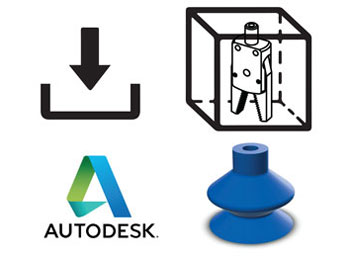
CAD File Downloads
Easy & Convenient! Our EOAT CAD Library has over 4,400 components and is updated daily. Download all or individual files, or preview them by Quick# with EMI’s 360° View before downloading.
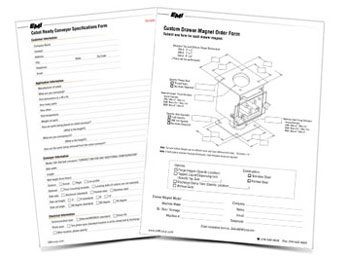
Reference & Forms
Our Interactive Forms are easy to fill-out and submit by email. Our Reference Pages contain important information on EOAT and Conveyor systems.